Best practices in stock management for small businesses
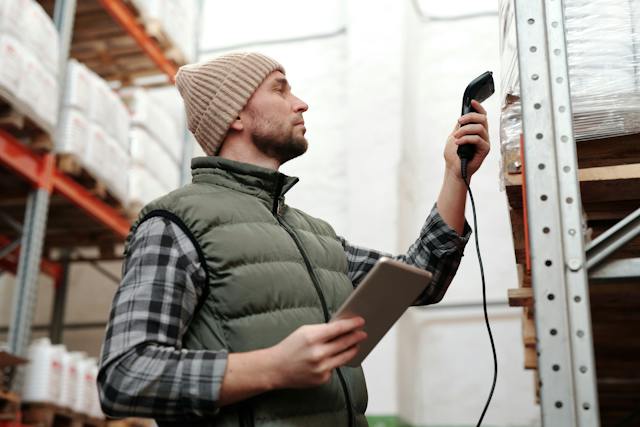

Stock management, a vital aspect for small businesses, involves acquiring, storing, and effectively utilising inventory. This process balances supply and demand, minimises costs, and avoids waste or loss. Small businesses, in particular, need more resources and efficient operations to manage their inventory.
Recent statistics highlight the significance and challenges of stock management for small businesses. Surprisingly, 43% of small businesses do not actively monitor their inventory, and 21% claim to have no stock at all, indicating a potential lack of focus on this crucial area. On the other hand, those who engage in inventory tracking commonly use accounting software as their primary method. This reliance on technology highlights the growing digitisation trend in stock management practices.
The global supply chain industry, integral to stock management, has a substantial market value of $15.85 billion and is expected to grow at a compound annual growth rate (CAGR) of 11.2% until 2027. This growth reflects the increasing complexity and importance of efficient supply chain management for businesses of all sizes.
Additionally, inventory models play a significant role in effective stock management. These models help businesses determine the optimal way to produce and manage goods, considering factors like industry specifics, production lifecycle, and investment maximisation strategies. For instance, complex manufacturing and supply chain processes often use methods like Just-In-Time (JIT) and Materials Requirement Planning (MRP).
The importance of stock management for small businesses must be considered. It’s a dynamic field influenced by technological advancements, global supply chain trends, and the evolving needs of businesses. Effective stock management is about having the right items at the right time and maximising resources, managing costs, and delivering quality goods to customers efficiently.
Understanding stock management
Stock management, often called inventory management, is essential for businesses of all sizes, particularly small ones. It involves overseeing and controlling the ordering, storage, and use of components that a company will use to produce the items it will sell and managing quantities of finished products for sale. Several key concepts are fundamental to understanding stock management:
- Inventory turnover: refers to the number of times a company’s inventory is sold and replaced over a period, usually a year. A higher inventory turnover indicates efficient selling of goods, while a lower turnover might suggest overstocking or market challenges.
- Order quantity: This involves determining the optimal amount of stock to order at a given time. It’s a balancing act between having enough inventory to meet customer demand and not overstocking, which can tie up a business’s cash flow.
- Economic Order Quantity (EOQ): EOQ is a formula used to identify the ideal order quantity that minimises the costs of ordering and storing inventory. It’s a crucial concept for effective stock management, helping businesses reduce costs while ensuring product availability.
- Safety stock: This is the additional quantity of an item held in the inventory to reduce the risk of stockouts caused by variations in supply and demand.
- Lead time: In stock management, lead time is the duration between placing and receiving an order. Businesses need to understand their lead times to make accurate inventory forecasts and avoid stockouts.
- Reorder point formula: This formula helps businesses determine the right time to reorder stock based on lead time and safety stock levels.
The difference between stock management and inventory control is subtle but important. While stock management encompasses the broader strategic approach of managing the inventory lifecycle, inventory control is more about the day-to-day management of stock levels, including tracking inventory, ensuring the right amount of product is available at the right time, and minimising costs associated with inventory, such as storage and loss.
Stock management and inventory control are critical for small businesses because they directly impact cash flow, operational efficiency, and customer satisfaction. Effective management of stock ensures that businesses can meet customer demands promptly, maintain a lean inventory, and optimise their supply chain processes.
Setting up your stock management system
Choosing the right stock management tools and software for small businesses
- Assess business needs: Before selecting a tool or software, evaluate your business’s specific needs, including the size of your inventory, variety of products, and budget constraints. Features to look for:
- Inventory tracking: Capabilities to track stock levels, sales, deliveries, and orders.
- Integration: Compatibility with other systems like accounting software and point of sale (POS) systems.
- User-friendly interface: Easy-to-navigate and user-friendly interface for efficiency.
- Reporting and analytics: Tools to analyse stock trends, sales patterns, and inventory forecasts.
- Scalability: Software that can grow with your business.
- Customer support: Reliable customer support for troubleshooting and guidance.
- Research and comparison: Look into various options available in the market. Compare based on features, costs, scalability, and user reviews.
- Trial periods: Take advantage of free trials to test the software’s compatibility with your business operations.
Steps for setting up a basic stock management system
- Inventory categorisation: Classify inventory into various categories for ease of management (e.g., fast-moving, slow-moving, perishable).
- Set up a stock database: Create a centralised database to record and track inventory details like stock levels, supplier information, and reorder points.
- Implement a reordering system: Establish a system for automatic stock reordering based on predefined reorder points to prevent stockouts.
- Train staff: Educate your team on the new system, emphasising the importance of accurate data entry and adherence to the system’s processes.
- Regularly update the system: Keep the system updated with new products, suppliers, and changes in inventory levels.
Best practices in stock management
Regular auditing
- Physical stock checks: Conduct regular physical inventories to verify the accuracy of stock records. This can be done annually, semi-annually, or quarterly.
- Reconciliation: Reconcile physical stock counts with recorded data in the stock management system. Investigate and rectify any discrepancies.
Accurate forecasting
- Historical sales data analysis: Use past sales data to predict future stock needs, considering seasonal variations and market trends.
- Stay informed of market trends: Keep abreast of industry and market trends that could impact demand for your products.
- Use forecasting tools: Utilise software tools that offer predictive analytics for more accurate forecasting.
Vendor management
- Build strong relationships: Develop strong relationships with suppliers for better negotiation power and reliability.
- Evaluate and select vendors: Carefully assess potential vendors based on reliability, quality, price, and delivery terms.
- Regular communication: Maintain regular communication with suppliers to stay updated on any changes that may affect your inventory.
Efficient ordering
- Economic Order Quantity (EOQ): Use the EOQ model to determine the optimal order quantity that minimises total inventory costs.
- Monitor stock levels: Continuously monitor stock levels to determine when reordering is necessary.
- Automate ordering processes: Implement automated ordering systems to streamline the process and reduce manual errors.
Contingency planning
- Identify risks: Identify potential risks such as supplier failures, stockouts, or market changes.
- Develop a response plan: Create plans for different scenarios, including alternative suppliers, emergency funding, and stock redistribution strategies.
- Regular review and update: Regularly review and update contingency plans to ensure they remain relevant and effective.
Effective stock management is a dynamic process that requires ongoing attention and adaptation. By implementing these practices, small businesses can create a robust stock management system that supports operational efficiency, financial health, and customer satisfaction.

Leveraging technology in stock management
Overview of technological solutions
- Radio-Frequency Identification (RFID):
- Function: Uses electromagnetic fields to identify and track tags attached to objects automatically.
- Benefits: Provides real-time tracking of inventory, reduces manual counting errors, and improves overall inventory visibility.
- Barcoding:
- Function: Uses barcodes and barcode scanners to track and manage inventory.
- Benefits: Simplifies data entry, enhances accuracy of inventory tracking, and speeds up the checkout and restocking processes.
- Inventory management software:
- Function: Software platforms that track inventory levels, orders, sales, and deliveries.
- Benefits: Offers centralised data management, improved reporting and analytics, and facilitates decision-making with real-time data.
- Cloud-based systems:
- Function: Host inventory management software on cloud servers, allowing remote access.
- Benefits: Enhances data accessibility and security, enables remote management, and provides scalability.
- Mobile inventory management:
- Function: Utilises mobile devices and apps for managing inventory.
- Benefits: Increases accessibility for on-the-go management, improves the efficiency of stock audits and allows for immediate updates.
- Automated reordering systems:
- Function: Automatically places orders for stock replenishment based on predefined criteria like stock levels or forecasted demand.
- Benefits: Prevents stockouts, reduces manual workload, and optimises stock levels.
- Integration capabilities:
- Function: Allows inventory management systems to integrate with other business systems like CRM, ERP, or e-commerce platforms.
- Benefits: Provides a holistic view of business operations, streamlines processes, and ensures consistency across different systems.
How technology can streamline stock management processes
- Enhanced accuracy: Technological tools like RFID and barcoding significantly reduce human error in inventory tracking and data entry.
- Efficient data management: Inventory management software centralises inventory data, making it easier to access, analyse, and manage.
- Improved visibility and control: Real-time tracking and analytics provide businesses with a clear view of their inventory levels, enabling better control over stock management.
- Time and cost savings: Automated processes and efficient data handling save time and reduce operational costs related to manual inventory management.
- Better decision making: With accurate data and advanced analytics, businesses can make informed decisions about purchasing, stocking, and sales strategies.
- Scalability: Cloud-based systems and software allow businesses to easily scale their inventory management system as they grow, without the need for significant infrastructure investment.
- Adaptability to market changes: Quick access to data and trends enables businesses to adapt rapidly to market demands or supply chain disruptions.
- Customer satisfaction: Efficient stock management leads to better order fulfilment, reduced stockouts, and faster delivery, all contributing to enhanced customer satisfaction.
Incorporating technology into stock management processes offers significant advantages for small businesses, allowing them to manage their inventory more efficiently and effectively while staying competitive in the marketplace.

Common challenges and solutions
Identifying and addressing common stock management challenges faced by small businesses
- Overstocking and understocking:
- Challenge: Balancing inventory levels to avoid excessive stock that ties up capital (overstocking) or insufficient stock that leads to stockouts and lost sales (understocking).
- Solution: Implement inventory forecasting tools and regularly review sales data to predict demand more accurately.
- Inaccurate inventory data:
- Challenge: Maintaining accurate inventory records, as discrepancies can lead to poor decision-making.
- Solution: Utilise barcoding or RFID technology for real-time inventory tracking and conduct regular audits for accuracy.
- Inefficient inventory processes:
- Challenge: Manual, time-consuming, error-prone inventory processes.
- Solution: Automate inventory processes with software that can manage orders, track inventory, and update stock levels in real-time.
- Cash flow management:
- Challenge: Investing too much in inventory can strain cash flow.
- Solution: Use inventory management techniques like Economic Order Quantity (EOQ) to optimise purchasing decisions and maintain a healthy cash flow.
- Vendor management and supply chain disruptions:
- Challenge: Managing supplier relationships and coping with supply chain disruptions.
- Solution: Diversify supplier base, maintain good communication with suppliers, and develop contingency plans for supply chain disruptions.
- Lack of real-time data and analytics:
- Challenge: Making informed decisions without access to real-time data.
- Solution: Implement cloud-based inventory management systems that offer real-time analytics and reporting capabilities.
- Limited resources and expertise:
- Challenge: Small businesses often have limited resources to invest in advanced stock management systems.
- Solution: Opt for scalable and affordable cloud-based solutions that offer essential features without the need for significant investment.
Practical solutions to overcome these challenges
- Utilise technology to automate and streamline processes.
- Regularly train staff on inventory management best practices.
- Keep abreast of market trends and adjust inventory strategies accordingly.
- Foster strong relationships with suppliers for better collaboration and reliability.
- Continuously review and adjust inventory management strategies based on business growth and market changes.
Effective stock management is critical for the success of small businesses. It involves maintaining optimal stock levels and encompasses aspects like supplier management, accurate forecasting, and leveraging technology for efficiency.
Key takeaways include:
- The importance of balancing inventory to avoid overstocking and understocking.
- The need for accurate data for informed decision-making.
- The role of technology in automating and streamlining stock management processes.
- The significance of strong supplier relationships and contingency planning.
Small businesses should view stock management as a dynamic and integral part of their operations. Continuous assessment and improvement of stock management practices are essential for adapting to market changes, meeting customer demands, and ultimately driving business success. Embracing these practices can lead to improved operational efficiency, enhanced customer satisfaction, and better financial health.